Automotive Sector:
The innovation Challenge
Automotive is generally synonymous with Technological Evolution. A sector and an industry that in order to be competitive needs a continuous updating of knowledge, know-how and solutions.
This is a must for companies along the the value (supply) chain. But the use of new knowledge and technologies – albeit driven by international “Key Players” – has a significant impact also on all of them.
Automotive: how has the traditional model changed?
The traditional model, in which the “Key Players” completely directed the innovation choices and the investment of the various suppliers in cascade – according to a pyramid model of product architecture – by financing the medium and long-term commercial risk with huge resources, has changed in recent years due to various factors of a strategic nature, but also of technical / financial sustainability on the part of the players in the sector.
In order to differentiate themselves, to be able to compete and better face increasingly open and international markets, some suppliers have acquired a greater autonomous ability to design and manufacture their own products and systems, others have tried to evolve from small product / process leaders to precise specifications. of customers, towards producers of more complex systems / subsystems, seeking greater added value and defending their economic autonomy.
Furthermore, in a sector characterized by huge investments and development costs, combined with a very distant break-even point in time and subject to large market uncertainties and volumes, companies have begun to adopt cooperative models of ‘risk sharing’ throughout the supply chain – both vertically and horizontally – and along all the phases, from design, to configuration, up to industrialization and production to production, becoming increasingly autonomous from the Prime on a technical and financial level, but also on a commercial one.
Innovation and the ability to support it with investments and own resources, instead of depending on the client / “Key Player”, has therefore become a competitive lever to improve both the performance of internal processes and the ability to develop intellectual property on one’s own, with an excellent level of performance that is adequate to the demands of the market.
This now allows supplier companies to participate in the evaluation system and accredit themselves to customers as long-term reliable partners.
Obviously, this paradigm shift requires companies to be willing to take risks and invest in human and financial capital. In many cases it will be necessary to identify and focus on technologies and solutions that are not yet fully available or in an immature stage – to be proposed to the market and used tomorrow – forgetting the ‘customer driven’ logic to move towards a logic of performance optimization and improvement continuous. But all this has a cost: it is necessary to allocate own and subsidized finance, access institutional and private co-investment programs, attack markets, customers and applications outside the local / domestic perimeter in order to maximize returns. And above all, acquire new technical and managerial / managerial skills.
Accept the challenge to innovate in the automotive sector
The reality and sustainability of the sector in CEE:
A network of SMEs rooted in the territory
The automotive ecosystem in the CEE region is made up of the majority of automotive key players ranging from VW, Audi, Skoda, Seat, Peugeot, Citroen, Jaguar Land Rover, up to Toyota, with Volvo entering Slovakia and BMW growing significantly in Hungary. They all respresent a huge part of CEE’s GDP and employ thousands of employees in the region.
On the other side of the spectrum, we have medium / small companies that are very different from each other in terms of positioning, but all strongly rooted in the territory. The dense network of interpersonal and professional relationships is still today the greatest facilitator of corporate collaborations and also of innovation processes. However, not all companies today are able to withstand international comparison with other leading companies in products and systems and not only because of their size; to this is added their prevailing dependence on the domestic market, the weakness of financial structures and, in many cases, the distance from operational excellence.
For companies focused on technology management – of which they are often considered among the most qualified leaders, excellent producers of products and components, capable of responding flawlessly to their customers’ specifications – the guidelines for innovation are:
- constant investments in process technologies to improve the performance of the cycle phases and product specialization;
- defense of the distinctive competencies of the company and consequently career development, especially for internal succession;
- commercial efforts to constantly search for new uses and new applications, both within the automotive sector and in other sectors, of existing products.
For companies that – in a proactive relationship with their customers – produce components or acquire them externally also through collaborations with other companies, the innovation guidelines are:
- investing in ‘intangible’ factors to develop design, innovation and implementation skills of complex systems, acquiring qualified technical resources, pushing on continuous training, personnel development, the transfer of knowledge within the company and with the external environment (universities, research centers, technology hubs, partners, etc.), the development of organizational structures that facilitate organizational learning and the creation of knowledge;
- create networks of stable technical / commercial collaboration that allow both to access critical resources and to contain the investments necessary for product development;
- develop financial management skills to access funds and financing, optimally allocate huge resources, but also efficiently control the different projects and contract budgets;
- strengthen technical / commercial and marketing skills in order to be able to operate on a variety of markets without almost ever assuming the dimension of a global competitor.
The macro trends of the future in the Automotive sector and the necessary skills to acquire
The Automotive sector is also undergoing strong transformations due to both the technological / digital trends in progress, and the emergence of new needs on the part of the Client which, in addition to the traditional objectives (performance, cost, speed, weight, etc. …), is increasingly attentive to issues of sustainability, decarbonisation, increase in IT costs (cyberattacks etc).
These innovations and technological developments represent the driving force for the evolution of the demand for new products and solutions expected in the coming years, but also for skills.
The macro-trends of the future for product innovation are:
- Advanced and urban air mobility
- Electric propulsion
- Autonomous / unmanned driving
- Hydrogen / biomass / syntetic fuel as alternative sources of energy and fuel
- UAVs / drones
- Microsatellites
- The new innovative materials (graphene, composite materials, …)
The macro-trends of the future for process innovation are:
- Automotion
- Virtual / augmented reality (AR / VR)
- 3D printing / additive manufacturing
- Digital twins simulation / design systems
What about the digitization of the automotive sector?
The automotive sector is capable of generating a huge amount of data. New technologies such as IoT, the Cloud, Artificial Intelligence, Cyber Security are sources of Big Data generation and application platforms for their processing for business purposes and process improvement.
Big Data and its management – from generation, to collection and analysis / capitalization – are increasingly essential and represent the foundation of the information architecture to derive information capable of driving innovations and changes. For example, to get to know your customers better, to optimize production processes, as well as those of distribution and maintenance, as well as to increase the overall quality of company services.
New organizational models for the automotive sector:
Rethinking teams to develop new capabilities
To manage these innovation trends internally and to seize the opportunities of new technologies on the market in parallel, it is necessary to think of organizational models based on the professionalization of roles, on the sharing of choices and on the contamination between different experiences and also open to the outside world and to Open Innovation.
The traditional specialized resources of automotive companies must be integrated / updated not only with the new necessary technical know-how, but also with new managerial, managerial and behavioral skills.
Certainly it is necessary to rethink the technical / technological teams, including, for example, new specialists in hardware / software development, programming, modeling and simulation, design and system engineering, materials engineering and advanced technologies; as well as strengthening skills in operations, on smart production methods and technologies, on manufacturing 4.0 or supply chain management.
In terms of managerial and managerial skills, project management and the coordination of transversal activities, the engineering and continuous improvement of business processes and organizational models, planning and control at all operational and financial levels, become increasingly important attitudes to leadership, results, team work and problem solving.
The same effort of reorganization and requalification requires a different planning capacity to understand the skills needs according to strategic positioning, define upskilling / reskilling and recruiting programs, establish attraction and retention plans for new talents.
In short, in order to ride the macro trends of innovation, the need to invest in the acquisition of skills that today are not yet so present in companies emerges strongly.
The transformation process towards new products / services, processes and technical / managerial skills in the various impacted areas (R&D, Manufacturing, Supply Chain, Planning, etc.) obviously starts from an awareness and strategic determination of the top management and / or of the Ownership , but it can pass from the use of external specialists with experience in change management, also coming from sectors other than aerospace and more advanced, who can accelerate this process by bringing solutions, transferring know-how.
Do you see a similar challenge at your company? Get in touch with me, I am more than happy to discuss and share my opinion.
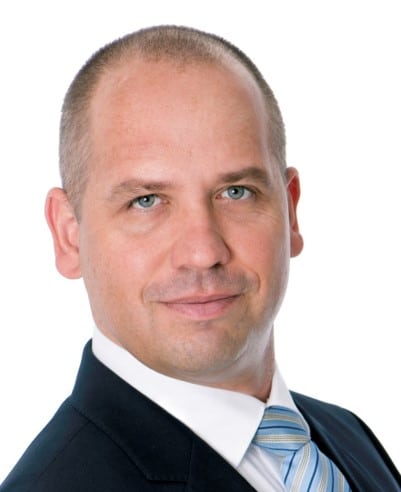
Bohuslav Lipovsky, Managing Partner
EIM Executive Interim Management CEE
Together we can find the solution you are looking for
About Bohuslav
Bohuslav has international experience, he has been active in interim management for several years, speaks several languages, and has extensive experience from numerous projects.